Wellhead gas refers to natural gas that is extracted directly from a well at its source, typically an underground reservoir. It is the gas that flows out of the wellhead immediately after drilling and completion operations. Wellhead gas is a mixture of hydrocarbons, primarily methane (CH4), along with small amounts of other gases such as ethane (C2H6), propane (C3H8), butane (C4H10), and various impurities like nitrogen (N2), carbon dioxide (CO2), and hydrogen sulfide (H2S).
After the well is drilled and gas is produced, the wellhead gas is typically collected and processed to remove impurities and separate the natural gas from other components. This processing may involve the removal of water, solids, sulfur compounds, and other contaminants to meet commercial specifications and safety requirements. The processed wellhead gas can then be transported through pipelines for distribution and use in various applications, such as heating, electricity generation, industrial processes, and as a fuel for vehicles.
Wellhead gas is an important natural resource and a primary source of energy worldwide. Its extraction and production are regulated by government authorities and industry standards to ensure safe operations, environmental protection, and the efficient utilization of the resource.
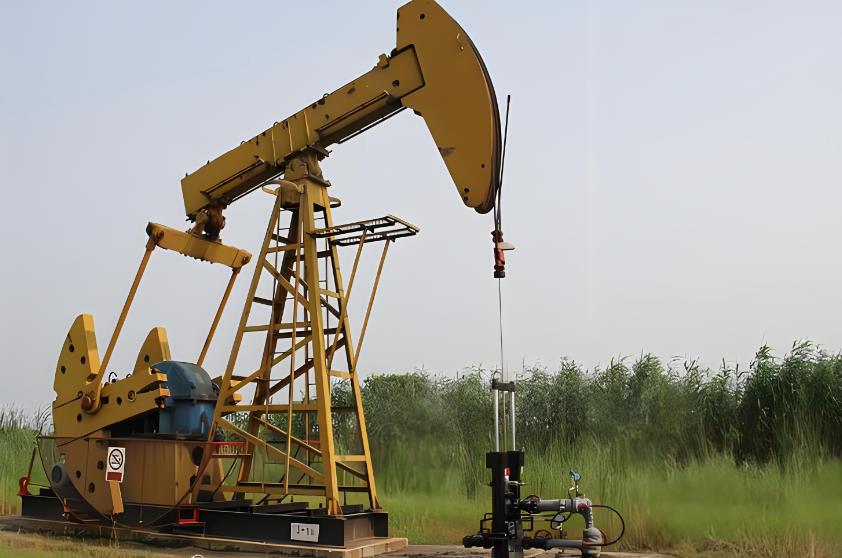
The primary function of a wellhead gas compressor is to increase the pressure of the natural gas extracted from a wellhead. This is achieved by compressing the gas using mechanical means. Here are the key functions of a wellhead gas compressor:
1. Pressure Boosting: The primary purpose of a wellhead gas compressor is to boost the pressure of the extracted gas. As gas flows from the wellhead, it typically experiences pressure losses due to friction, distance, and other factors. The compressor increases the gas pressure to overcome these losses, ensuring efficient and effective flow through the production and transportation system.
2. Flow Control: Wellhead gas compressors help regulate the flow rate of the gas. By increasing the pressure, the compressor helps maintain a consistent and controlled flow rate. This is important for optimizing production levels, meeting downstream process requirements, and ensuring reliable transportation through pipelines or other systems.
3. Gas Gathering: In situations where multiple wells are connected to a central gathering system, wellhead gas compressors are used to gather the gas from individual wells. By creating sufficient pressure, the compressor collects gas from multiple wells and transports it to a centralized point for further processing or distribution.
4. Gas Conditioning: Wellhead gas often contains impurities such as water vapor, liquid hydrocarbons, and other contaminants. Wellhead gas compressors can be equipped with additional components, such as separators, coolers, and filters, to remove these impurities and condition the gas for further processing or transportation.
5. Gas Compression for Storage: In some cases, wellhead gas may be compressed and stored in underground storage facilities for future use during periods of high demand or as a reserve. Wellhead gas compressors are employed to increase the gas pressure for effective storage and subsequent withdrawal as needed.
6. System Stability: Compressors contribute to the stability of the gas production and transportation system. They help compensate for variations in wellhead gas production rates and changes in downstream demand, ensuring stable flow conditions. This prevents issues such as flow disruptions, pressure drops, or fluctuations that could impact the overall system performance.
7. Energy Efficiency: Wellhead gas compressors are designed to operate efficiently, aiming to minimize energy consumption while achieving the required compression ratio. This helps optimize the energy efficiency of the gas production and transportation system, reducing operational costs and environmental impact.
The specific design and configuration of wellhead gas compressors can vary based on factors such as well characteristics, production requirements, and transportation systems. Compressor systems may include multiple stages, various control mechanisms, and safety features to ensure reliable and efficient operation.
There are various types of wellhead gas compressors available, each designed to meet specific operational requirements and conditions. The choice of compressor type depends on factors such as gas composition, flow rate, pressure requirements, and site-specific considerations. Here are some common types of wellhead gas compressors:
1. Reciprocating Compressors: Reciprocating compressors are widely used in wellhead applications. They use pistons driven by a crankshaft to compress the gas. Reciprocating compressors can be single-acting (compression on one side of the piston) or double-acting (compression on both sides of the piston). They are known for their high efficiency and flexibility in handling various pressure ratios and gas compositions.
2. Screw Compressors: Screw compressors use two interlocking helical rotors to compress the gas. As the rotors rotate, the gas is drawn in, compressed, and discharged. Screw compressors are known for their smooth operation, high reliability, and ability to handle a wide range of gas compositions. They are often used in wellhead applications with moderate to high flow rates.
3. Centrifugal Compressors: Centrifugal compressors rely on centrifugal force to compress the gas. Gas enters the compressor at the center and is accelerated by a high-speed impeller. The kinetic energy is then converted into pressure energy as the gas is forced through diffusers. Centrifugal compressors are suitable for high flow rates and can handle large volumes of gas. They are commonly used in wellhead applications with high-pressure requirements.
4. Rotary Vane Compressors: Rotary vane compressors use a rotor with vanes that slide in and out of slots to compress the gas. As the rotor spins, the vanes trap and compress the gas. Rotary vane compressors are compact, simple in design, and suitable for low to moderate flow rates. They are commonly used in smaller-scale wellhead applications or in situations where space is limited.
5. Liquid Ring Compressors: Liquid ring compressors utilize a liquid ring formed by a rotating impeller to compress the gas. The gas is drawn into the compressor and trapped in the liquid ring, where compression occurs as the impeller rotates. Liquid ring compressors are known for their ability to handle wet or saturated gases and are commonly used in wellhead applications where there is a presence of liquid or condensate in the gas stream.
It's important to note that the suitability of each compressor type depends on the specific requirements of the wellhead operation, such as gas composition, flow rate, pressure conditions, and operational constraints. Consulting with compressor manufacturers or industry experts can help determine the most appropriate compressor type for a particular wellhead application.
The pricing of wellhead gas compressors can vary significantly depending on several factors, including the compressor type, capacity, specifications, and customization options. Additionally, market conditions and supplier pricing policies can also impact the cost. Therefore, it's important to contact compressor manufacturers or suppliers directly for accurate and up-to-date pricing information.
However, to provide a general idea, here are some approximate price ranges for wellhead gas compressors:
1. Reciprocating Compressors:
- Smaller reciprocating compressors (lower capacity): $10,000 to $50,000 USD
- Medium-sized reciprocating compressors: $50,000 to $200,000 USD
- Larger reciprocating compressors (higher capacity): $200,000 to $1 million+ USD
2. Screw Compressors:
- Small to medium-sized screw compressors: $50,000 to $300,000 USD
- Larger screw compressors (higher capacity): $300,000 to $1.5 million+ USD
3. Centrifugal Compressors:
- Small to medium-sized centrifugal compressors: $100,000 to $500,000 USD
- Larger centrifugal compressors (higher capacity): $500,000 to $2 million+ USD
4. Rotary Vane Compressors:
- Smaller rotary vane compressors: $5,000 to $20,000 USD
- Medium-sized rotary vane compressors: $20,000 to $100,000 USD
5. Liquid Ring Compressors:
- Small to medium-sized liquid ring compressors: $10,000 to $50,000 USD
- Larger liquid ring compressors (higher capacity): $50,000 to $300,000 USD
Please note that these price ranges are approximate and can vary significantly based on factors such as compressor size, capacity, features, and customization requirements. It's always recommended to consult with compressor manufacturers or suppliers to obtain accurate pricing based on your specific needs and project requirements.